Metoda skutecznej ochrony przed korozją poprzez pokrycie konstrukcji powłoką metaliczną cynkową, aluminiową czy cynową. Metalizacja zanurzeniowa, zwana także ogniową, polega na umieszczeniu konstrukcji, po wcześniej odpowiednio przygotowanej powierzchni, w wannie ze stopionym metalem lub stopem. Metoda jest dość tania, a uzyskane powłoki metalowe charakteryzują się dobrą odpornością na korozję, odpowiednią grubością o dyfuzyjnym połączeniu z podłożem.
Wstępne przygotowanie podłoża przed kąpielą zanurzeniową składa się z kilku etapów:
- usuwanie zanieczyszczeń, płukanie,
- odtłuszczenie, płukanie,
- trawienie, płukanie.
Tak przygotowane elementy przechodzą do topnikowania. Ma ono za zadanie pokryć szczelnie podłoże aby nie zachodziły reakcje utleniania. Dodatkowo spełnia zadanie dotrawiające jeśli nie wszystkie zanieczyszczenia zostały usunięte. Celem topnikowania jest także poprawa zwilżalności podłoża i jego aktywacja przed kąpielą w ciekłym metalu.
Do topnikowania używa się najczęściej mieszaniny ze związków: chlorków cynku, cyny, amonu, potasu oraz tleneku boru. Substancje te charakteryzują się niskim napięciem powierzchniowym.
Po zakończeniu topnikowania, elementy są osuszane przed ostatnim etapem technologicznym. Kąpiel w wannie metalizacyjnej, to ostatni krok. Etap, w wyniku którego otrzymujemy powłokę metalową w zależności od zawartości wanny (cynkowanie, ołowiowanie, cynowanie, aluminiowanie lub ich stopy). Powłoka powstająca przy zanurzeniu konstrukcji ma budowę warstwową. Na grubość powłoki wpływa temperatura kąpieli, czas jej trwania i skład materiału elementu.
Cynkowanie ogniowe
Budowa powłoki cynkowej jest warstwowa. Ze wzrostem warstwy maleje zawartość żelaza i zmniejsza się potencjał. Schemat przekroju powłoki cynkowej na rysunku poniżej.

Temperatura kąpieli waha się w granicach 440°C – 480°C. Czas zanurzenia trwać może od kilku sekund do kilkunastu minut i zależy od masy elementu. W skład kąpieli wchodzi:
- czysty cynk;
- dodatki poprawiające własności powłoki tj. np. Al – redukuje ZnO do Zn, czyli sprawia, że kożuch na powierzchni kąpieli znika, Sn – wpływa na przyczepność i gładkość powłoki oraz zatrzymuje wzrost warstw stopowych;
- zanieczyszczenia tj. Fe (żelazo) – jako pozostałość po kąpieli innych elementów powoduje powstawanie warstw twardego cynku czy Pb (ołów), który zmniejsza płynność kąpieli.
Wymagania dotyczące powłok cynkowanych zanurzeniowo określa norma ISO 1461. Dokument podaje własności powłok, określa wygląd, grubości, naprawy i przyczepność powłoki cynkowej do podłoży stalowych i żeliwnych.
Norma zaleca, aby wygląd powłoki cynkowej określać z odległości przynajmniej 1 metra. Należy pamiętać, że powłoki cynkowe otrzymywane metodą zanurzeniową nakładane są głównie w celach ochronnych i estetyka jest mniej ważna, chyba że strony ustaliły inaczej.
Powłoka może mieć delikatne wzgrubienia i miejsca o różnych odcieniach szarości, które mogą się układać we wzory tzw. kwiaty cynkowe. Zdjęcia poniżej, to przykłady akceptowanego pokrycia.
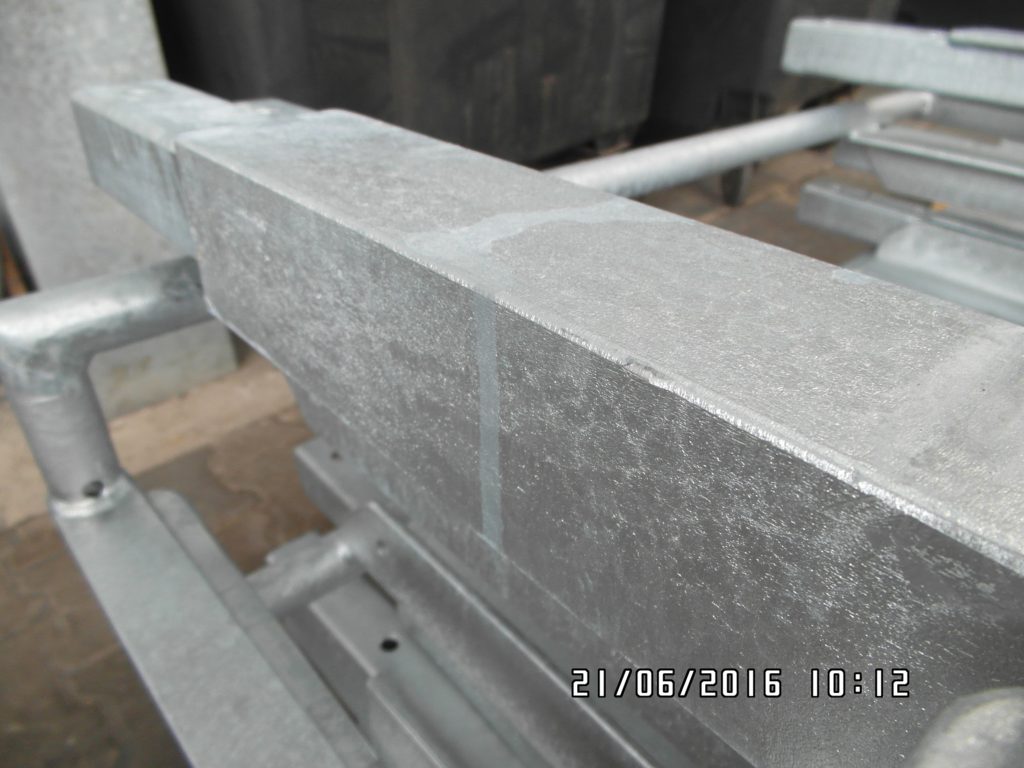
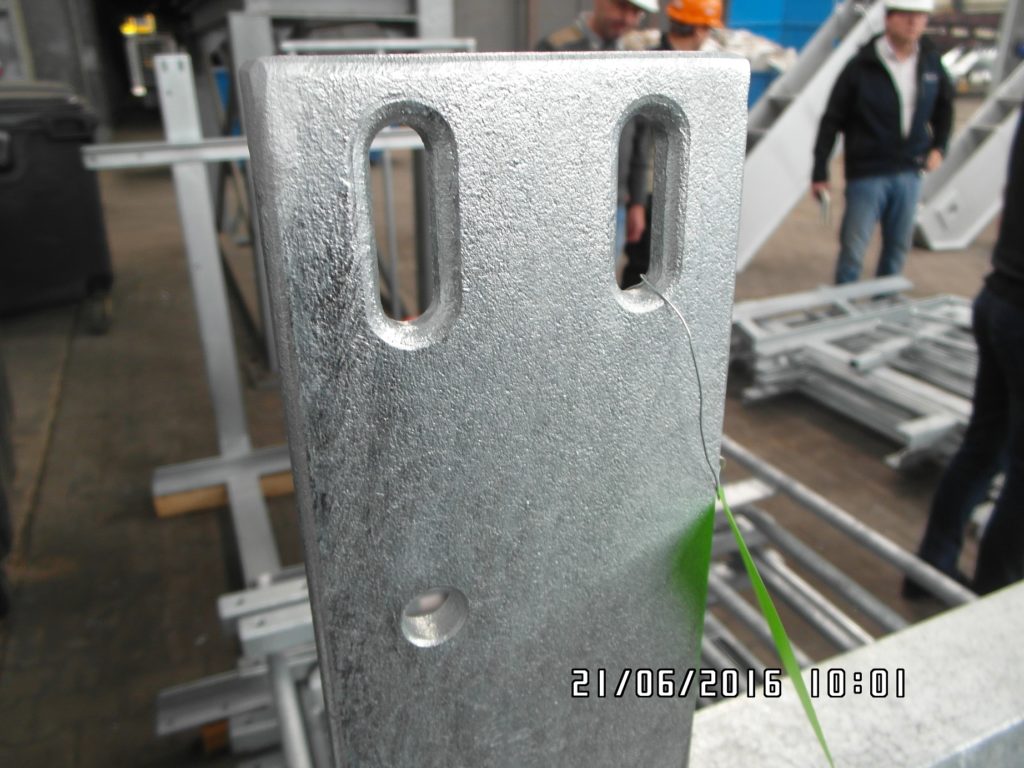
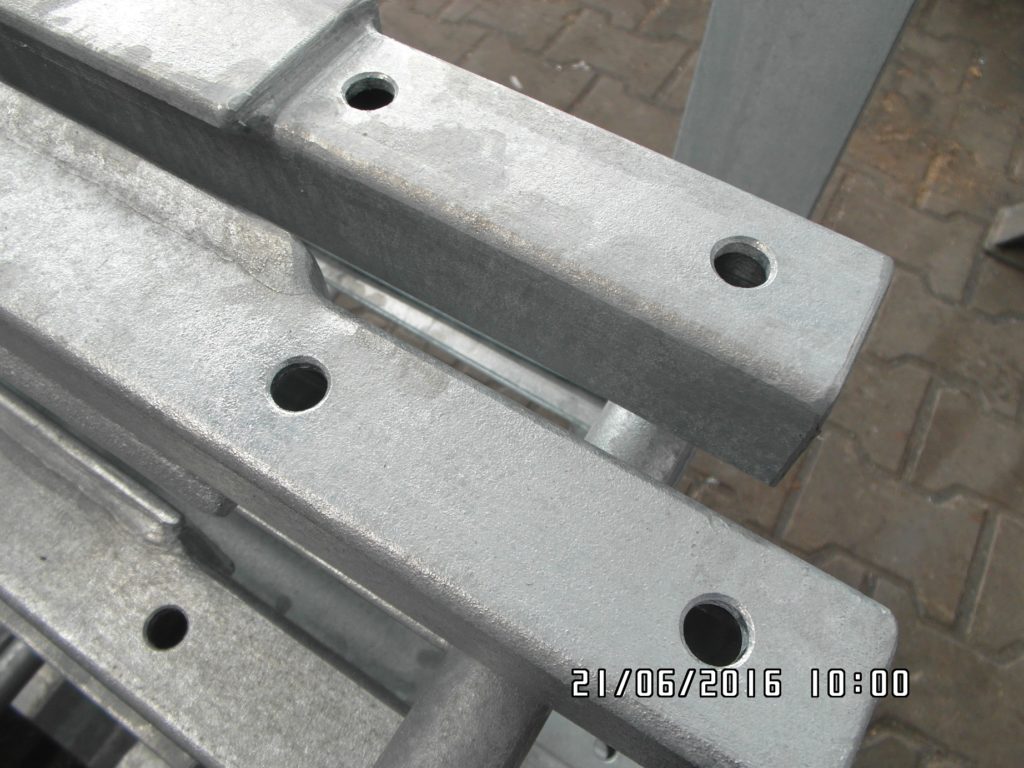
Wady mogące występować w powłoce cynkowej:
- zgrubienia, pęcherze,
- nawisy cynku,
- miejsca niepokryte powłoką cynkową,
- miejsca chropowate,
- pozostałości topnika i popiołu cynkowego,
- odspojenia powłoki od podłoża.
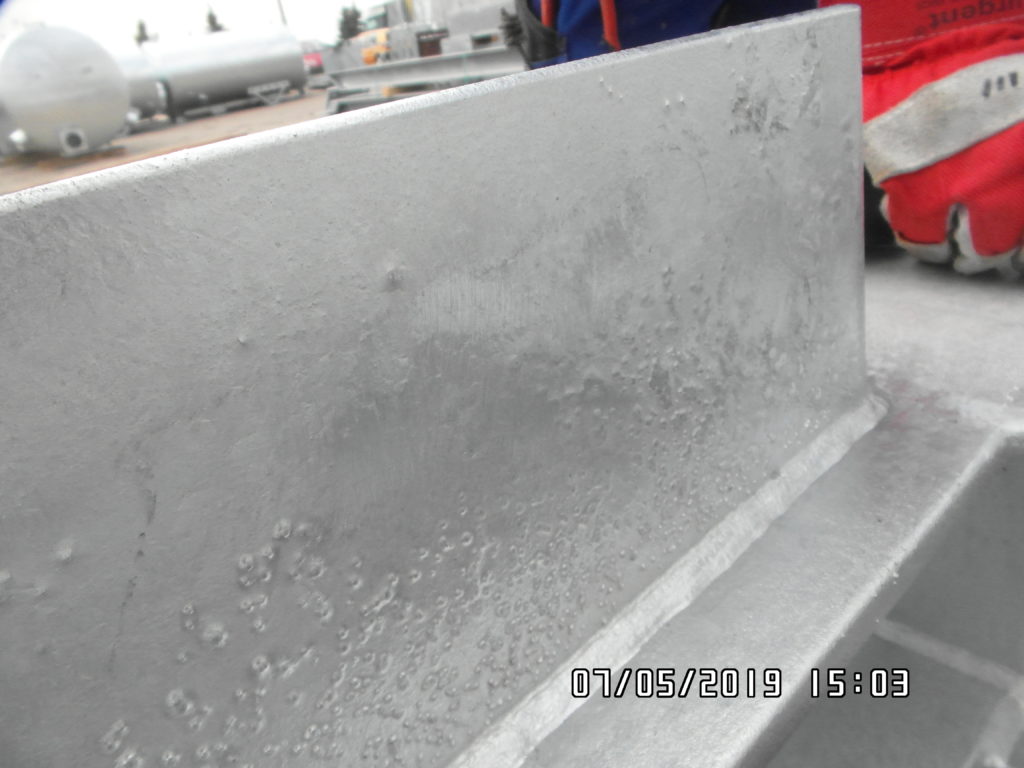
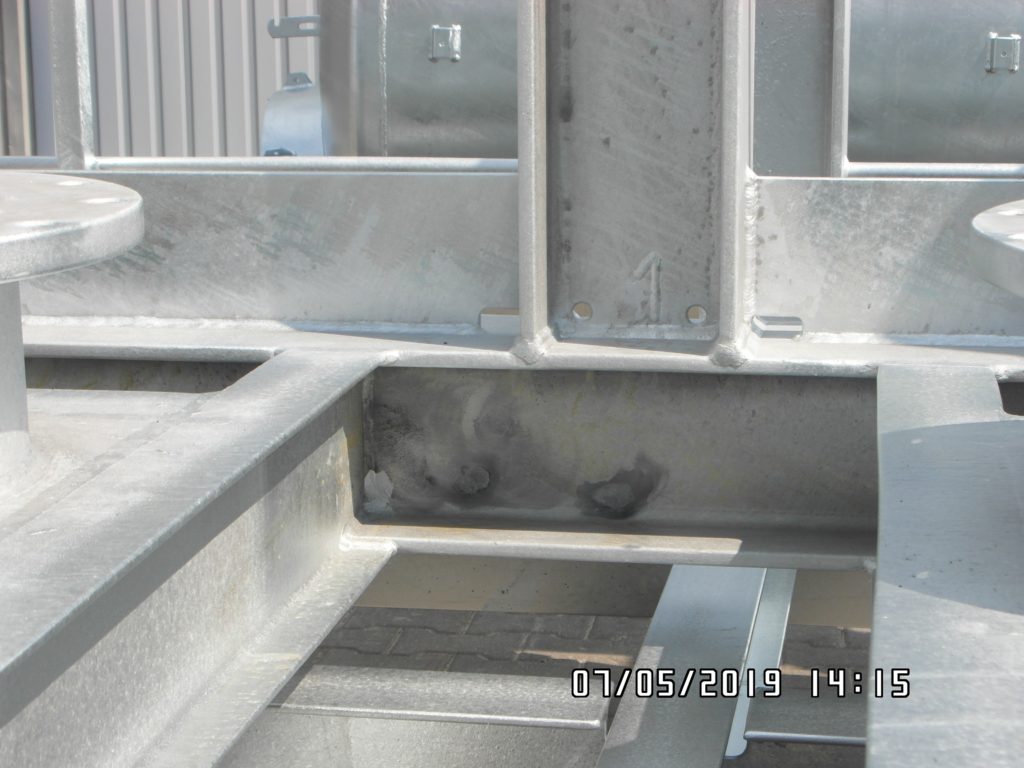
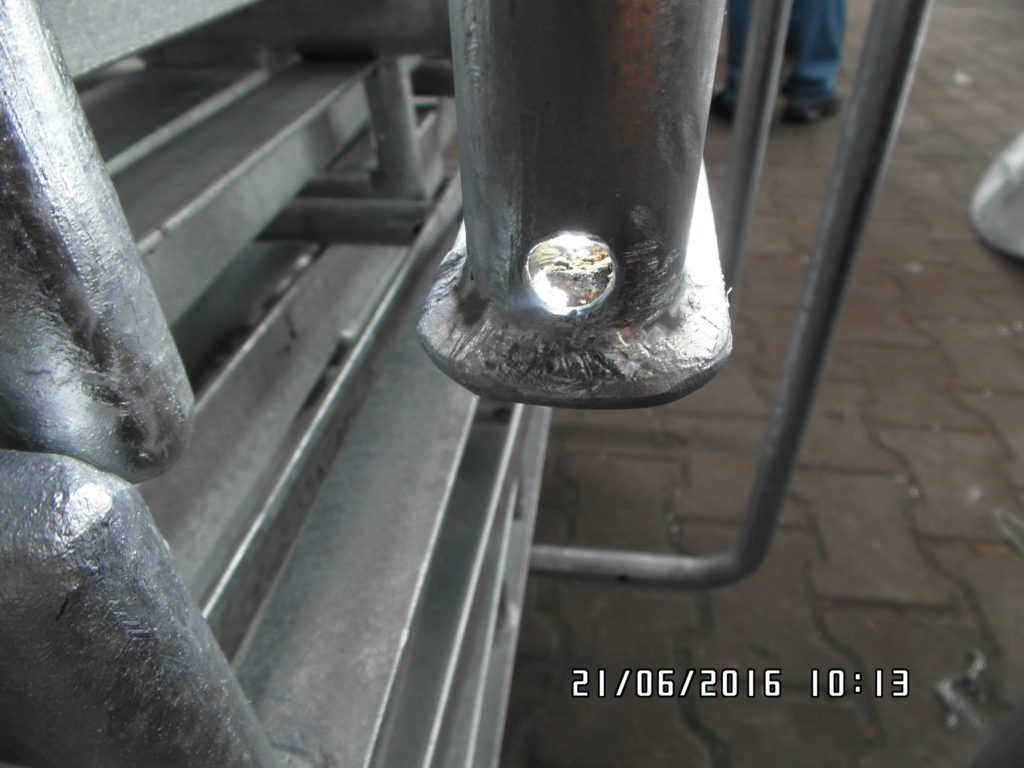
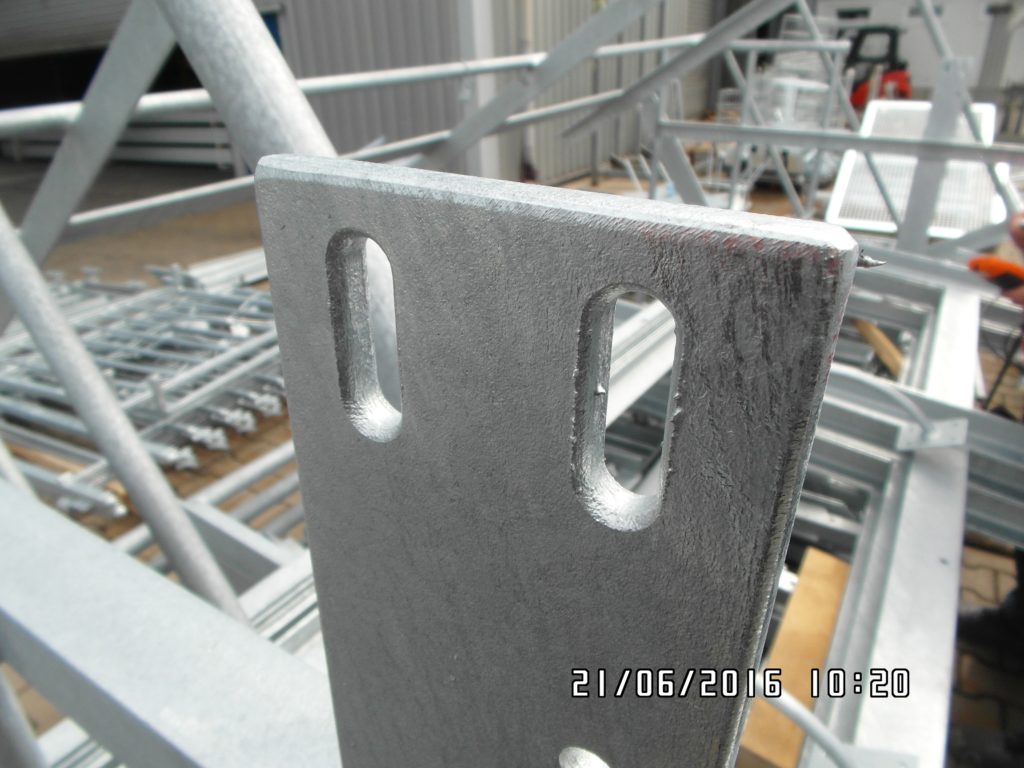
Uwaga! Według normy, suma obszarów nieocynkowanych, które będą naprawiane nie może przekroczyć 0,5% powierzchni cynkowanego detalu. Ubytki punktowe można uzupełniać poprzez: natryskiwanie cieplne, nakładanie powłok wysoko cynkowych, past cynkowych czy lutowanie. Jeżeli pojedyncze miejsce niepokryte powłoką cynkową ma powierzchnię powyżej 10 cm2, to element należy zawrócić do powtórnego cynkowania.
Elementy przeznaczone do cynkowania powinny być przygotowane do tego procesu. Konieczne jest zapewnienie otworów umożliwiających dopływ/odpływ płynnego cynku oraz odpowietrzenie. Detale muszą mieć ustalone punkty podwieszania.
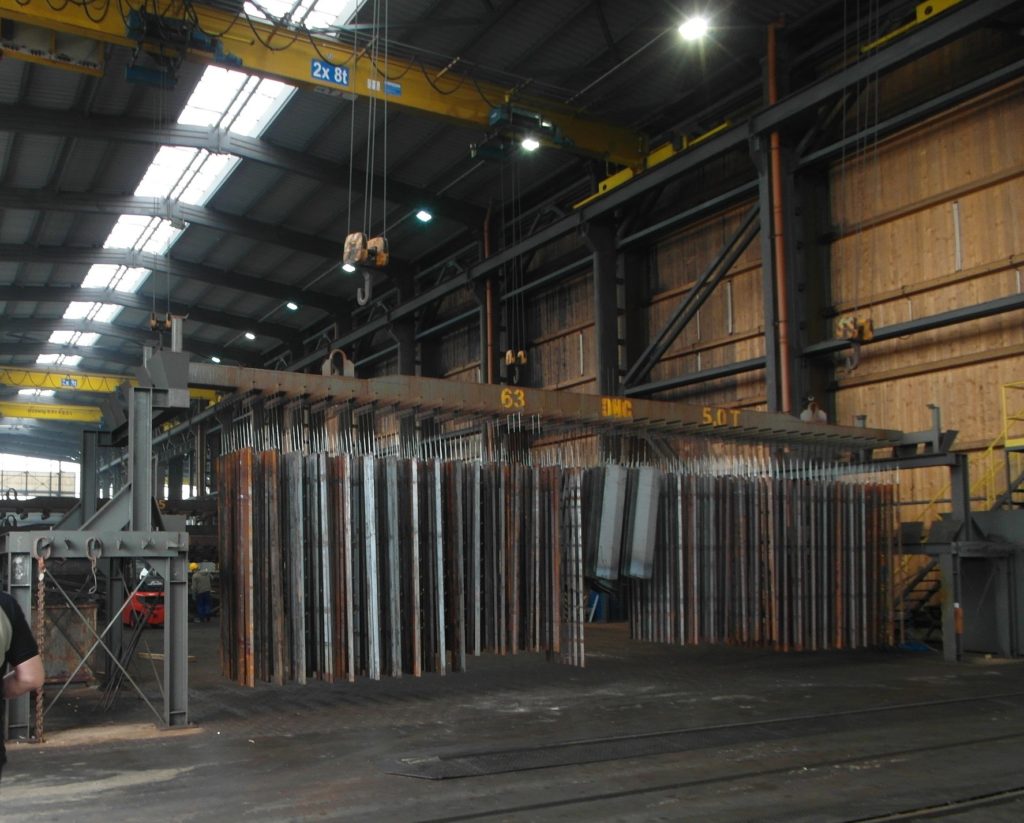
Elementy w wannie. Wyciąganie detali z kąpieli cynkowej.

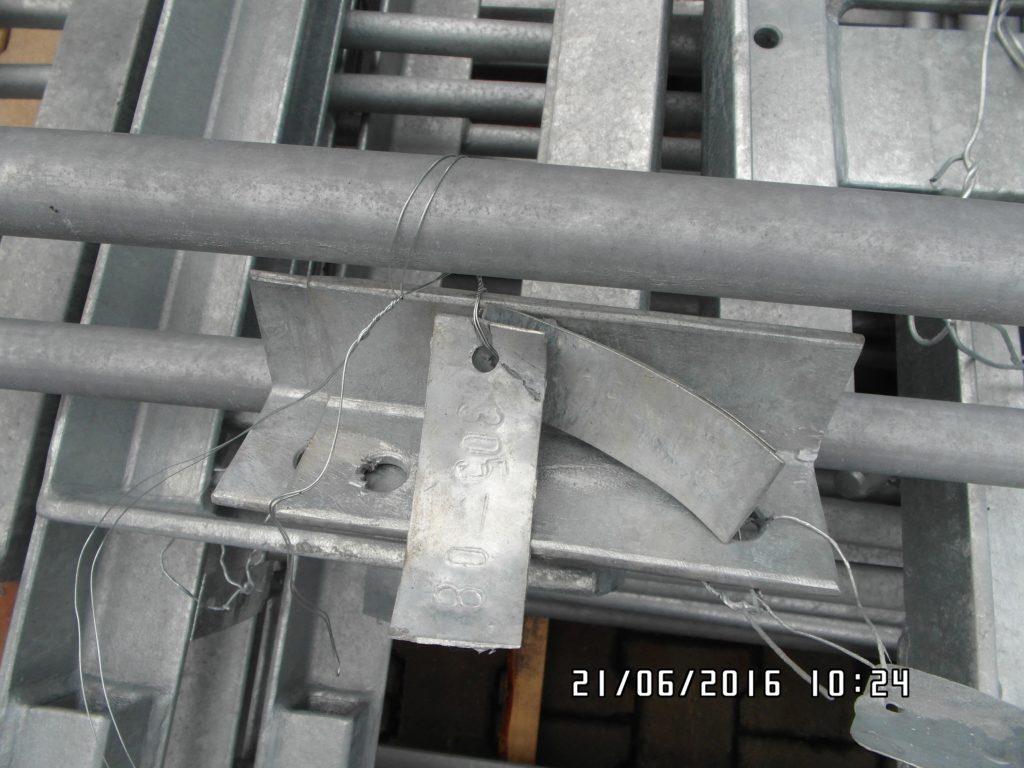
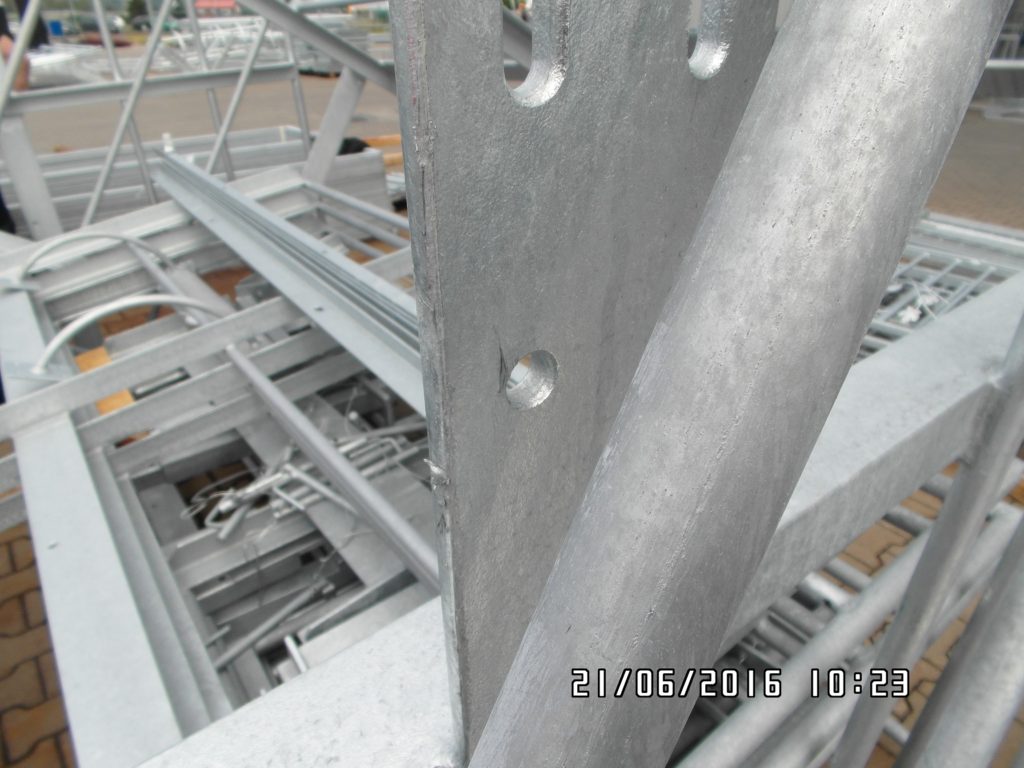
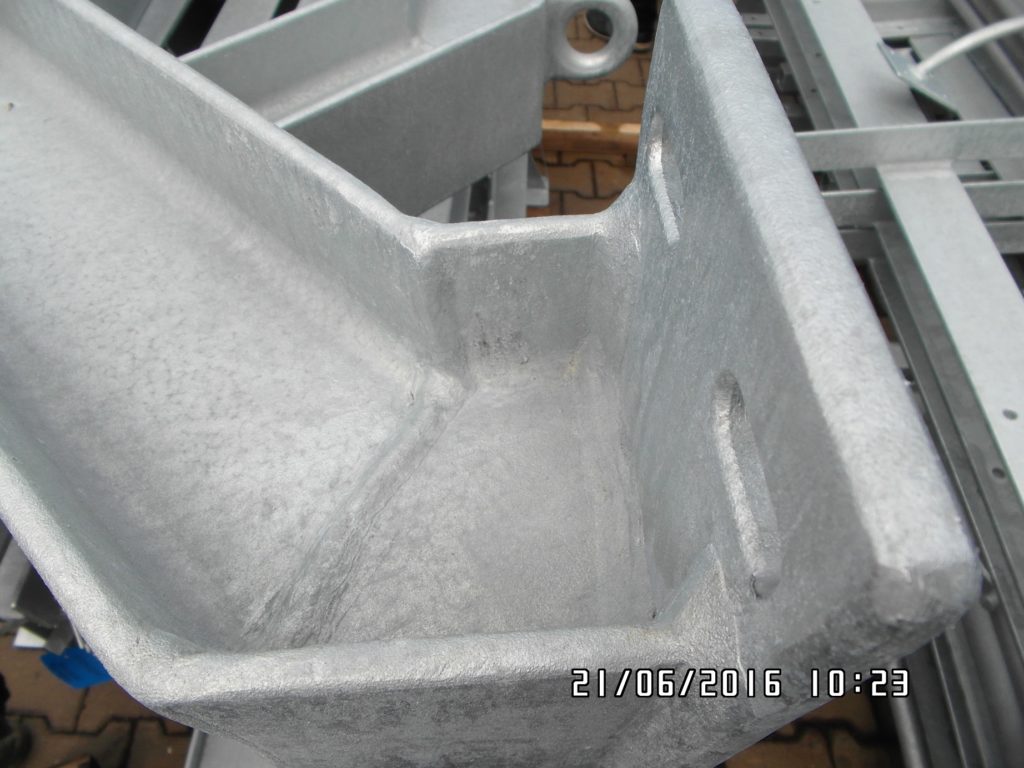
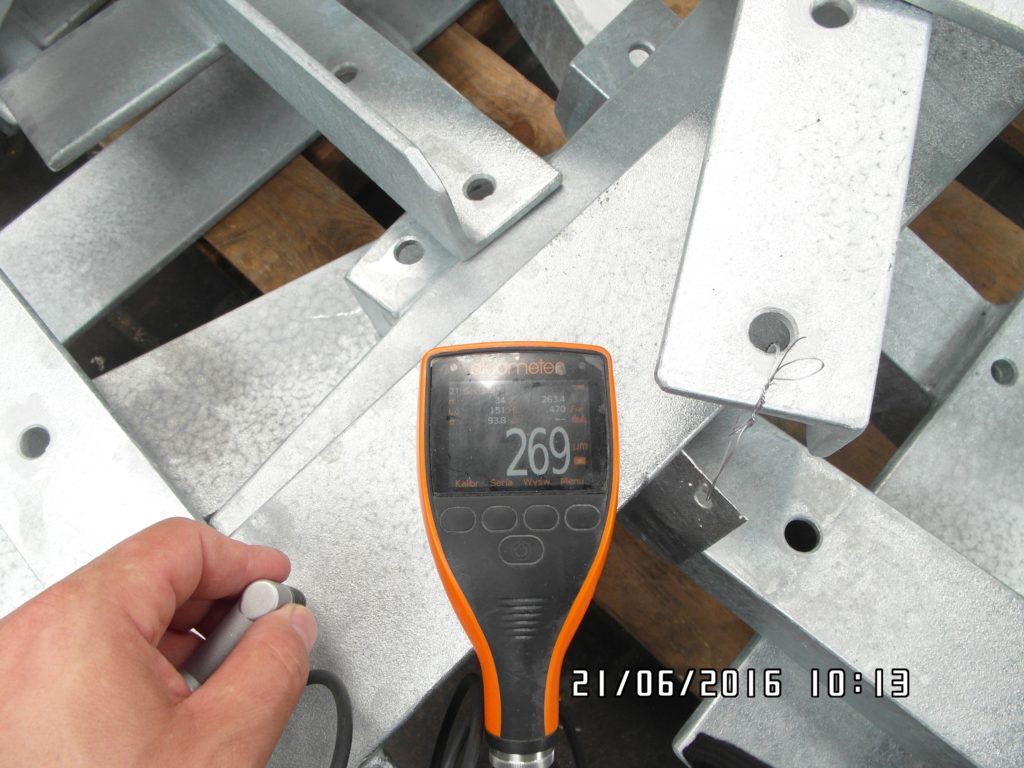
Ciekawostka! Zawartość Si (krzemu) i P (fosforu) w stali determinuje wygląd i skład powłoki cynkowej. Zawartość poniżej 0,03% daje powłokę srebrno – metaliczną, lśniącą o normalnej grubości. Większa ilość, oznacza powłokę cynkową bardziej szarą, matową. Powoduje przyspieszoną reakcją cynku z żelazem i zwiększoną grubość pokrycia. Przydatność stali do cynkowania ogniowego opisuje norma ISO 10025.
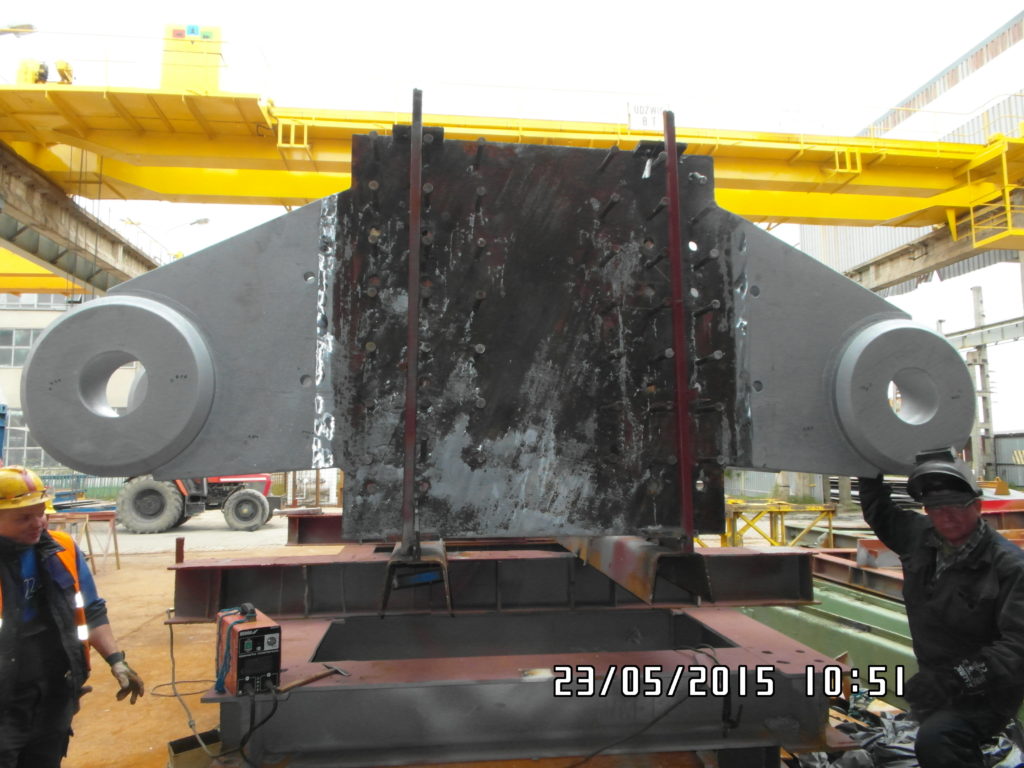
Ciekawostka! W zależności od charakteru konstrukcji, czasami cynkowanie ogniowe jest najprostszym sposobem zabezpieczenia. Brama na fotografii poniżej jest przykładem takiego wyjścia.
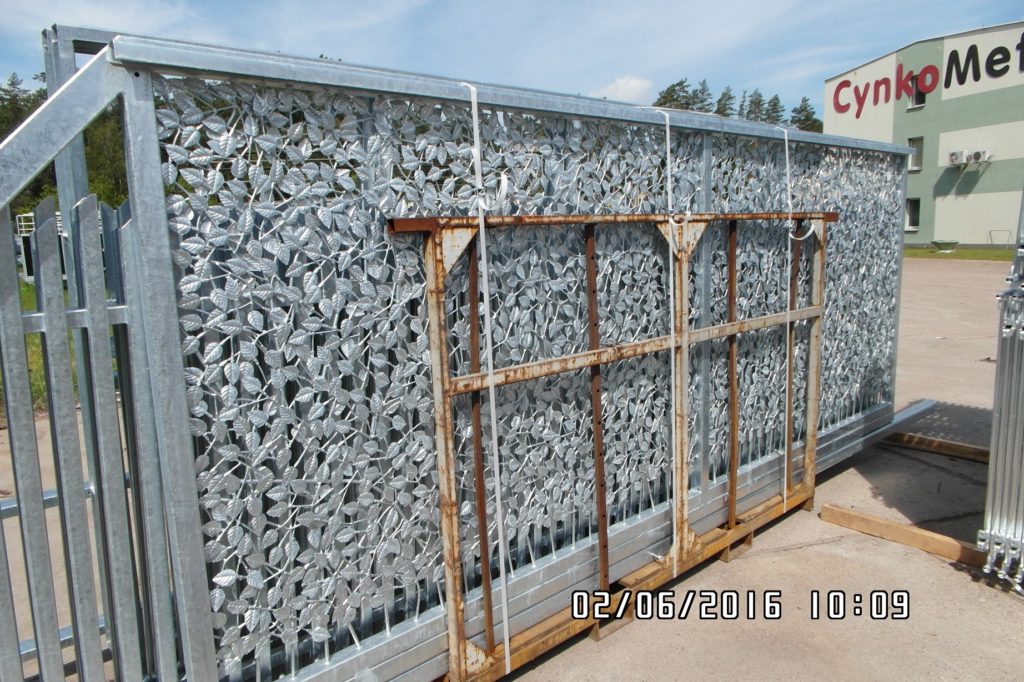